Il legno lamellare
L'evoluzione della tecnologia
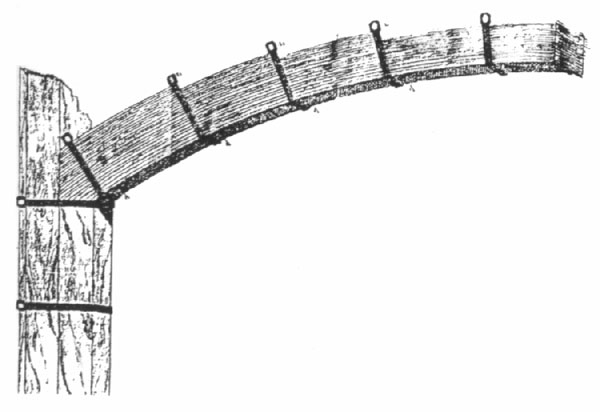
I PRECEDENTI STORICI DEL LEGNO LAMELLARE
Agli inizi del novecento un maestro carpentiere Svizzero di Weimar, Otto Helzer, ebbe la geniale intuizione di sostituire ai mezzi di collegamento meccanici una colla a base di caseina.
Nacque così il legno lamellare incollato, così come oggi si intende, ed il procedimento fu brevettato dall’inventore, in Austria ed in Svizzera, nel 1905.
Altri precedenti storici, richiamati da alcuni studiosi, non possono riferirsi in senso stretto alla attuale tecnologia.
Essi, infatti, riprendevano la tecnica costruttiva dell’arco in pietra, per realizzare strutture formate da elementi in legno profilati secondo superfici curve, con giunti sfalsati e chiavi di serraggio tra singoli elementi.

In Francia, Philipe Delorme fu tra i primi a proporre l’uso di tavole accoppiate a coltello per impiegarle nella copertura di grandi luci.
Delorme, pensò di trasferire al legno ciò che era noto per le costruzioni in pietra: la forma ad arco.
Propone, in pratica un arco con lamelle disposte a coltello tenute a pressione da tiranti in legno.
(Immagine Philibert Delorme, XVI sec.)
Il primo trattato che si occupa in Italia degli archi in lamellare risale al 1700. A Firenze, G. Del Rosso illustra la costruzione di ponti in legno con archi in lamellare tenuti a pressione per mezzo di fasce metalliche. Si riporta un brano del testo: ” L’arco è costruito nella seguente maniera.
Fatta una centina di piallacci di legno si farà centinare addosso alla medesima una fascina di abete grossa due quattrini di braccio. Sopra a questa se ne incolla una seconda e si ferma con degli stecchi dell’istesso legname. Sopra a questa se ne pone un’altra coll’istesso metodo e consecutivamente tante altre quante bastino per fare la grossezza che si vuole che abbia quest’arco, avvertendo di spartir bene le commettiture di dette assicelle, talché non cadano una di dritto sopra l’altra; la colla sia della massima forza e prenda per tutto; gli stecchi siano molti e per quanto risulta possibile, i buchi da fare col succhiello non si riscontrino con quelli di sotto.
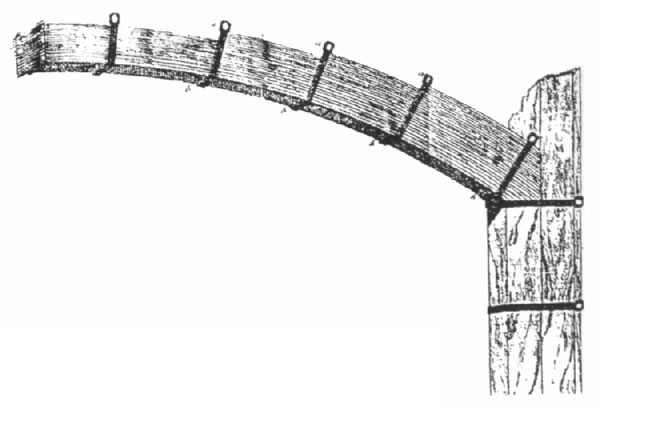
Finalmente essendo così terminato l’arco vanno fatti in varie distanze delle imbracature in ferro che vadano bene al centro fortemente serrate coi suoi paletti di sopra, acciocché’ non si possano separare e quest’arco. Sarà di una forza sorprendente.”
1797 – G. Del Rosso, Gran Ducato di Toscana, proposta di ponte composto con assicelle.
Cronologia di autori e proposte che hanno segnato l’evoluzione del concetto della ricostruzione di una trave, con elementi base ridotti, fino al brevetto di Hetzer.
E’ interessante notare come tutte le proposte si riferiscono all’arco; forse perché particolarmente adatto alle grandi luci.

L’evoluzione della tecnologia degli archi lamellari, principale tecnica costruttiva a cui ci si riferiva fino agli inizi di questo secolo per coprire grandi luci, ha seguito quattro principali teorie dovute a Delorme, Emy, Migneron, Wiebeking.
Nel sistema Emy le tavole venivano disposte come si fa attualmente e formavano un vero e proprio arco in legno lamellare come oggi siamo abituati a vedere.
A sinistra: G. Del Rosso, sezione maestra di una nave in legno. Al centro: copertura ad arco in legno lamellare progettato dal colonello Emy nel XIX secolo. A destra: arco con il sistema Emy; particolare costruttivo. (Click sulle immagini per ingrandire)
Il sistema di Migneron, prevedeva un arco con lamelle formate da travi curvate freddo. Alquanto simile era anche il sistema Wiebeking, che impiegava travi piegate a freddo e tenute a pressione da staffe metalliche e cunei in legno che evitavano possibili scorrimenti. Sempre nel secolo scorso, l’ingegnere tedesco Moller ideo’ una struttura simile a quella di Migneron e Wiebeking’ ma con l’introduzione fra gli elementi in legno di cunei che miglioravano l’inerzia della sezione.
Nell’immagine a sinistra: il ponte sul Rio Nuovo a Venezia, costruito da Eugenio Miozzi nel 1932.
La scelta del legno, cioè di una struttura leggera e resistente, fu determinata dalla necessità di contenere le spinte su una spalla dove si innestava un altro ponte. Tutt’oggi la struttura, nonostante le impegnative condizioni ambientali svolge il suo servizio.
Nell’immagine a destra: un capannone realizzato interamente in legno lamellare in provincia di Brescia nel 1939, apparteneva alla ditta ” Legnami Pasotti”.
IL PROCESSO DI PRODUZIONE
Il materiale
Per la fabbricazione dei manufatti in legno lamellare incollato sono generalmente impiegate tavole di legno di conifera (specialmente abete rosso, ma anche abete bianco e pino silvestre) dello spessore di 38 mm, larghe 10-24 cm e lunghe 4-6 metri. Le tavole sono accuratamente selezionate, eliminando quelle che presentano in maniera troppo diffusa i difetti più gravi o bonificando, ove possibile, i difetti più lievi e circoscritti.
Le tavole vengono quindi essiccate artificialmente, in appositi forni, per portarle ad un tasso di umidità relativa fra il 7 ed il 15%. Il valore è scelto in base alle condizioni di esercizio previste per il manufatto finito in modo da raggiungere quelle condizioni di equilibrio fra materiale e ambiente tali da non comportare alterazioni dimensionali. Vengono adottati quindi i valori di umidità relativa più alti per i manufatti destinati all’aperto o comunque esposti alle intemperie, quelli più bassi per i manufatti destinati ad ambienti chiusi e riscaldati.
La formazione delle lamelle
All’uscita dell’essiccatoio, dopo un periodo di stabilizzazione, inizia la lavorazione per la formazione delle lamelle. Tale lavorazione ha luogo su una vera e propria “linea automatica”, non dissimile dalle catene di produzione caratteristiche di altri materiali e manufatti. Si inizia con il controllo dell’umidità di ogni tavola; tale controllo ha luogo con strumenti ti elevata precisione (con una tolleranza ammessa del ± 3% rispetto ai valori prestabiliti), grazie anche al limitato spessore delle tavole (mm 38) rispetto ai legni segati di uso corrente nell’edilizia.
Le tavole che rientrano nella norma sono quindi “intestate” (cioè tagliate per rifinire le estremità) e fresate per realizzare i giunti “a pettine”. Tale operazione è particolarmente importante perché tale giunto aumenta la superficie di incollaggio di testa fra tavola e tavola e la sua configurazione deve corrispondere, là dove esistono, a precise normative (ad esempio la norma DIN 1052 tedesca).
Attraverso l’incollaggio dei giunti la tavola diviene “lamella”, la cui lunghezza non è più soggetta ad alcuna limitazione (a differenza. come si è detto, del legno segato massiccio) se non a quelle derivanti dalla possibilità di lavorazione nello stabilimento e di trasporto fino al luogo di impiego. Le lamelle così costituite sono quindi rettificate e piallate per unificarne lo spessore (dai 30 ai 35 mm) e vengono fatte “maturare” per consentire l’indurimento dei giunti.
La formazione dei manufatti
A seconda delle indicazioni progettuali, si procede alla formazione dei “pacchetti” di lamelle, dell’altezza e della forma voluta.
Le lamelle sono immesse in una incollatrice a fili che sparge su una sola faccia l’apposita colla.
La colla deve realizzare un collegamento meccanico quanto più possibile simile a quello esistente fra due strati di fibre del materiale originario.
Le colle usate sono essenzialmente di due tipi: all’urea-formaldeide per i manufatti destinati ad ambienti chiusi e protetti; – alla resorcina per manufatti destinati ad ambienti umidi od all’aperto. Le colle alla resorcina presentano una buona resistenza meccanica e stabilità all’invecchiamento; inoltre una buona resistenza ad acidi, alcali deboli, solventi, umidità, microrganismi, intemperie, acqua bollente e calore. Anche gli incollaggi devono corrispondere alle norme esistenti (ad esempio, per la Germania, le norme DIN 68141 e DIN 68705). Le singole lamelle cosparse di collante sono trasportate sul letto di pressaggio, tipo orizzontale, nel quale sono sovrapposte, nel numero desiderato, “di coltello”; una serie di profili metallici verticali mobili. disposti ad interasse di cm 40 esercita la opportuna pressione sul pacchetto di lamelle (generalmente 7 kg/cm2).
Il tempo di indurimento della colla è funzione della temperatura dell’ambiente e dell’umidità del legno e deve essere conforme alle istruzioni dei fabbricanti delle colle; generalmente esso può variare dalle 16 alle 20 ore. La configurazione geometrica del letto di pressaggio consente di ottenere elementi lineari o ricurvi, a seconda delle esigenze progettuali.
La norma DIN tedesca prescrive che il raggio di curvatura sia maggiore o uguale a 200 volte lo spessore delle lamelle (in pratica, maggiore o uguale a circa 6 m). Terminato l’indurimento della colla, hanno luogo le operazioni di finitura: piallatura sulle quattro facce, taglio a misura, sagomatura e forature previste per le connessioni metalliche, impregnazione.
Gli impregnanti, pigmentati o meno, costituiscono una difesa contro gli agenti patogeni (muffe. funghi, insetti). La dimensione dei pezzi finiti ha i seguenti limiti (sezione rettangolare): – larghezza: cm 8-22, pari a quella delle tavole ( tale larghezza può essere aumentata affiancando due tavole di larghezza diversa)I – altezza: fino a cm 198 (tale limite è dovuto soltanto alle possibilità di lavorazione delle macchine) -lunghezza: teoricamente infinita, anche se esistono le limitazioni per la lavorazione in stabilimento e per il trasporto.
Bibliografia: ARLUNNO G. – BAROSSO L. – LUCAT M.
Legno lamellare
Collegio degli ingegneri di Milano
Milano 1983
BENEDETTI C. – BAGIGALUPI V.
Legno e architettura
Kappa
Roma 1991
BETTONI G. – MARCHI G.
Strutture in legno per coperture di grandi luci – cenni storici
Collegio degli ingegneri di Milano
Milano 1977
LANER F.
Il legno lamellare. Il progetto.
Habitat legno
Brescia 1988
TROTTA G.
Considerazioni sul trattato
“Della facile costruzione dei ponti in legno”
Palutan
Milano 1983
Puoi scaricare la tavola in formato dwg
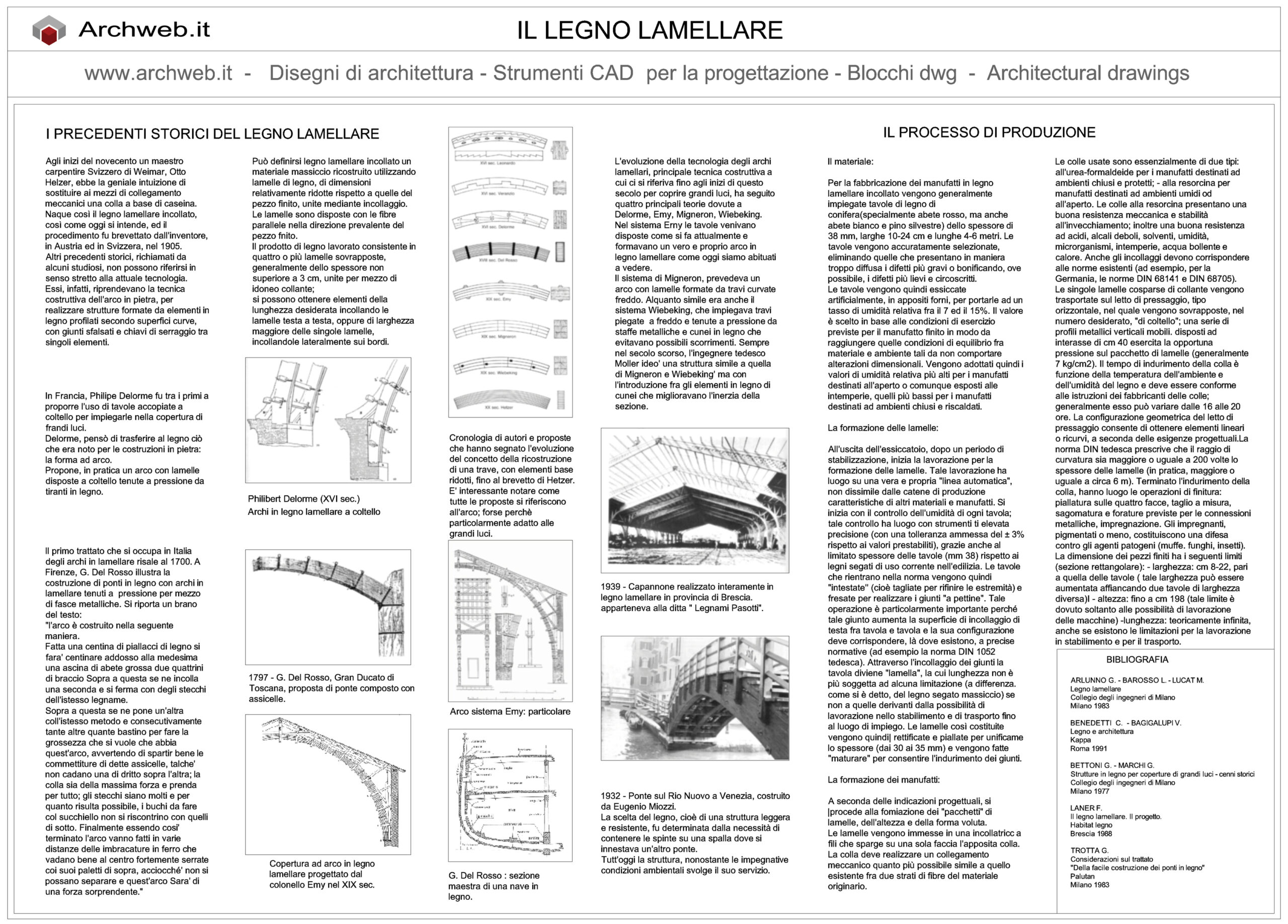